CASTINGS
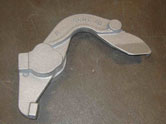
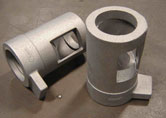
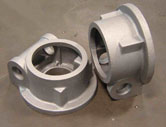
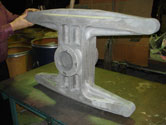
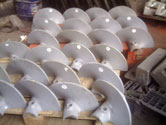
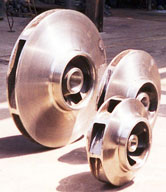
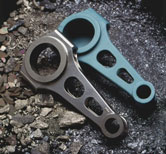
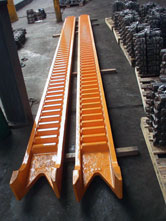

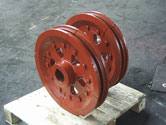
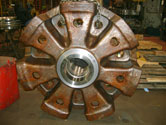
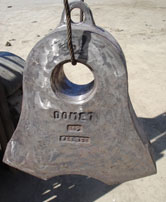
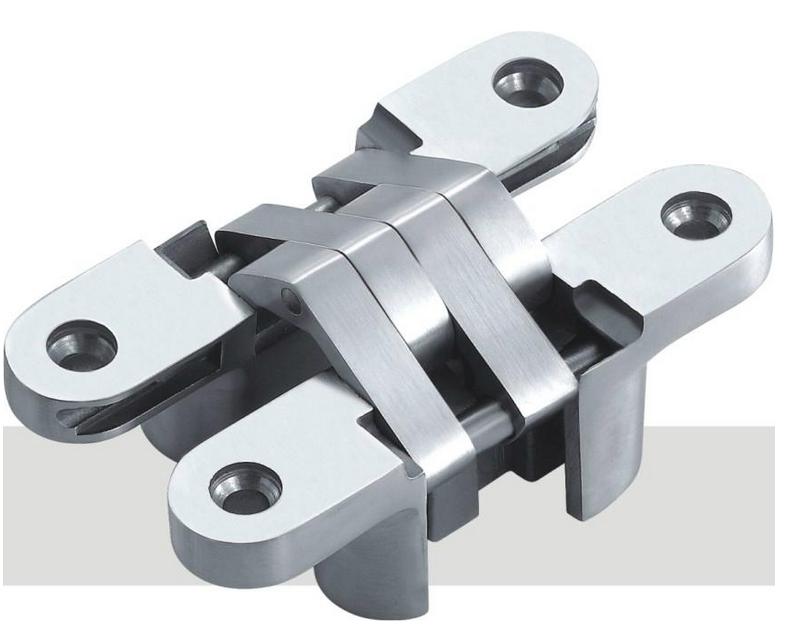
Castings
can be produced from any metal that retains a shape at ambient temperatures.
These forms are most commonly created through pouring molten metal into a
consumable sand-molded cavity made by pattern tooling. Casting has several key
advantages. It creates a part to near-net shape based on design criteria.
Casting also provides a cost-effective and easily repeatable alternative to
other manufacturing processes such as fabrication or machining.
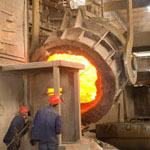
The procurement of castings presents many challenges for purchasing departments due to the myriad manufacturing processes utilized today. Without a thorough understanding of these casting methods, it is easy to become confused when selecting the best process and supplier to meet your requirements. A&T has the experience and knowledge to assist with identifying the best process to meet your needs at the best possible price. Below are a few of the molding methods we employ today to satisfy our customers' demands.
Green Sand — Process that mulls raw sand, clay and water, which is then compacted around a pattern to create a mold. Most common type of molding, suitable for any production volume, and typically a low-cost option.
![]()
![]()
No Bake / Airset — Molding method utilizing raw sand combined with resins and binder to create a hard mold capable of improved surface finishes. Excellent for lower-volume parts where superior dimensional stability is required.
Shell — Resin-coated sand, typically of a smaller grain size than green and or no bake sand, which is applied to a heated pattern that activates the resin to create a hard-shell mold. Exceptional surface finishes can be achieved with reduced machine stock and/or draft.
![]()
Investment — Casting process in which wax replicas are coated with a slurry mix of ceramic refractory and sand, allowed to dry, and then heated to extract the wax, leaving behind a near-net-shape cavity. Capable of creating shapes that are not possible by any other molding method, particularly for small or intricate components. Widely used to eliminate additional machining expense.
Lost Foam — Can be utilized in two different methods; The first method is similar to investment, in which a polystyrene replica is coated with ceramic refractory and then molded in sand. The second method consists of foam patterns that are molded into a media similar to no bake or airset. In either method, molten metal is poured directly into the sand mold and evaporates the foam during the casting process, creating a part with no draft or parting lines.
Permanent Mold — Reusable metal tooling that can be used to create repeatable dimensional accuracy, typically used for decorative or ornamental products made from nonferrous materials.
Die Cast — Method in which molten metal is forced into a metal die under pressure. This process is suitable for repeatability of medium- to high-volume, intricate or close-tolerance parts.
Centrifugal — Process utilizing permanent tooling that is rotated while molten metal is introduced, typically used to manufacture pipe or other cylindrical products.
V-Process — Dry sand molding method that uses a vacuum to hold a membrane on the surface of the pattern, which is then backfilled with sand. Advantages are exceptional surface finish and tighter dimensional control than most conventional sand casting processes.
Cores
are used when a casting design has a geometric profile that cannot be produced
using standard pattern tooling alone. The most common uses of cores are to form
internal passages or exterior features such as recesses or non-draft surfaces
that cannot be drawn from the pattern. A variety of core manufacturing methods
exist, however, the determination of which process to use has many factors,
including size, surface finish, cost and design requirements of the part. The
manufacturing of cores requires additional tooling (corebox) that can be made
from wood, metal or plastic. The major core processes are as follows:
Isocure (Cold Box) — This type of core making mixes dry sand with two types of resin just prior to use. After the mixture is blown into the corebox, a catalyst is introduced that causes an instant bonding of the resins.
Shell (Hot Box) — The shell process combines premixed sand with resin prior to being blown into a heated corebox. The heat melts the resin, binding the sand together.
No Bake — Very similar to Isocure, except that the resin and catalyst are introduced to the sand simultaneously and the mixture must be formed immediately.
After castings are produced, the important finishing processes of shakeout, cleaning and grinding begin. Shakeout is the removal of the castings from the mold, typically by a vibratory or rotary method. After shakeout, all gates and risers are removed from the casting during cleaning, typically using some type of abrasive media such as steel shot or ceramics. The grinding process involves removal of all detrimental fins, riser connections or other unwanted protrusions, and can be a manual or automated operation.
After all finishing is complete, castings are inspected to appropriate customer requirements such as visual defects, dimensional accuracy or non-destructive test methods to assure customer satisfaction. Upon completion of all finishing and inspection operations parts are packaged to customer specification, which can include quantity, arrangement and any protective packaging that may be required.
The A&T ADVANTAGE is that we offer unmatched resources and solutions to reduce the cost and frustration of purchasing castings. This is accomplished by applying our 300-plus years of foundry experience toward solving your casting issues. Our team is capable of assisting with all areas of the design and manufacturing process, including material selection to ensure critical design characteristics and identifying the appropriate process to provide the quality product you require. We also aid in design for manufacturability to keep production costs to a minimum and can help with converting expensive fabrications into reliable one-piece castings. A&T delivers value to our customers by ensuring consistent supply of the highest-quality part at competitive prices.
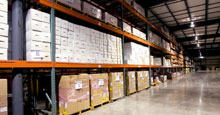
A&T also offers customer solutions to real-world issues such as small-quantity order requirements or guaranteed on-time delivery. This is typically achieved with Kanban or customized stocking/inventory arrangements, resulting in cost savings, reduced warehouse requirements and delivery in days rather than weeks.
In today's uncertain economy, many castings users are finding their supply chains interrupted as a result of sudden foundry closings, causing a potential shortage of raw material. Similarly, if you have an unexpected need for castings with a compressed lead time,A&T offers a rapid recovery solution to prevent avoidable, costly downtime in your system.
By incorporating A&T into your supply chain, you can eliminate the cost of identifying and managing multiple suppliers of castings. We offer a unique approach to the sourcing of castings by providing a reliable single-source solution to satisfy the most demanding requirements. Let us demonstrate how the A&T ADVANTAGE can improve your business by providing quality castings and the lowest total cost of ownership with our signature customer service.